Table of Content
Using your weeding tool or pen, weed the excess vinyl that you don’t want to be transferred to your garment. Vinyl cutter – A vinyl cutter takes computer files with patterns and letters and cuts them on a PU sheet or vinyl roll. By connecting a USB cable to a vinyl cutter, the machine will know what shape to cut. Design software – Unless you plan to purchase pre-made graphics, you’ll need to create your own. You can opt for paid apps like Adobe Photoshop with advanced features for sophisticated graphics or free-to-use apps like Canva or GIMP that also work well. Can of spray adhesive – if you want to reduce the possibility of your screen moving while on your t-shirt, apply a light coat of adhesive to your t-shirt beforehand.
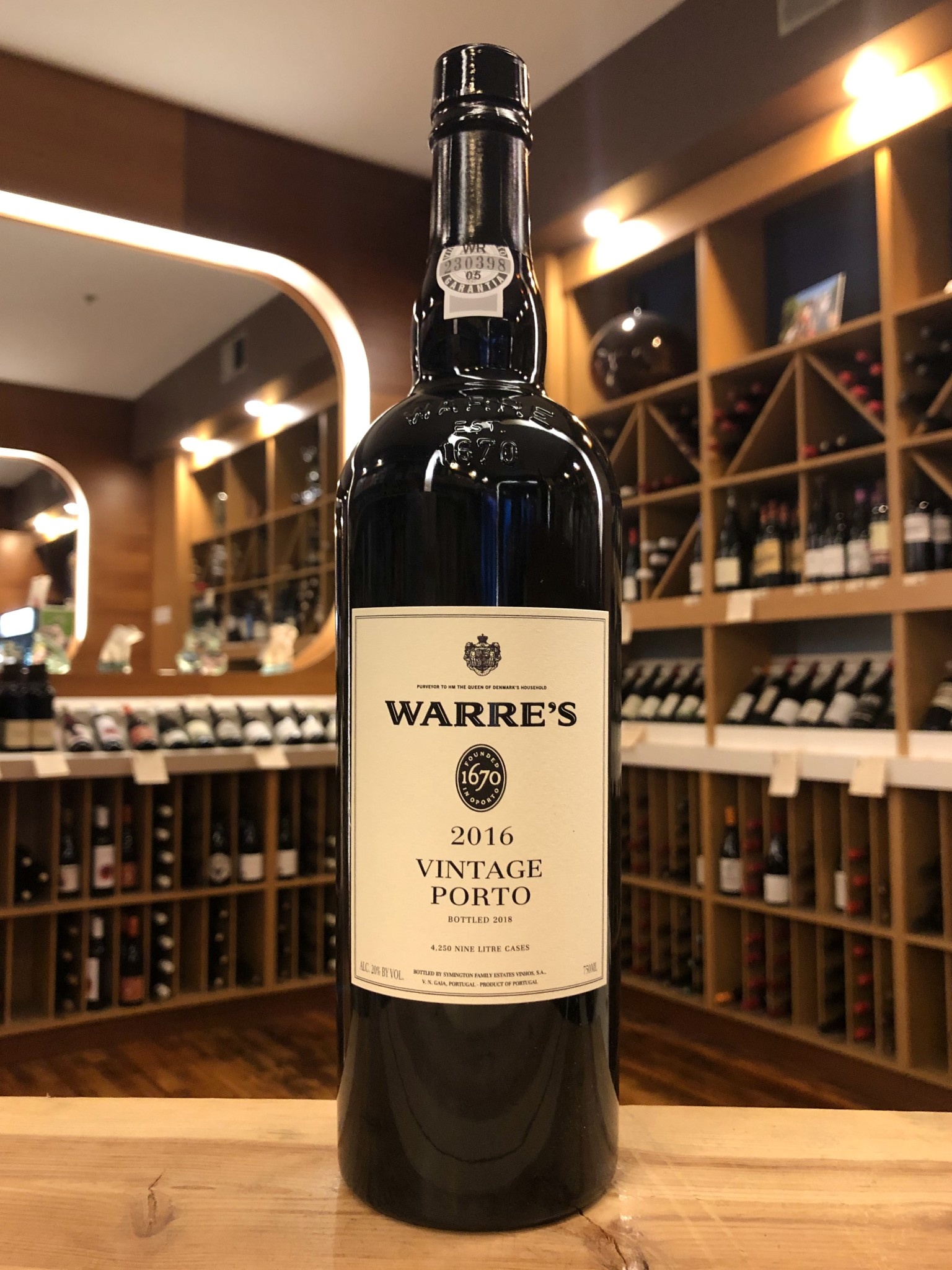
For an even bleach line, reload your brush every two inches. The fabric will quickly soak up the liquid so work quickly, but with a steady hand. Secure the shirt to the cardboard with elastics or small clips. This will keep the cardboard from slipping while you bleach paint. Test the paint by gently touching the painted spots.
Transfer Your Image:
You can download your preferable design from the internet, or you can create your own using illustrator or photoshop. All you need are a couple of tools and an instructional guide to making your own t-shirt design. But here we are about to share the easiest and most interesting one. Once 20 seconds have passed, pull the t-shirt out of the heat press and check to ensure that the design has not smeared or is still see-through. If it is, then put it back in for another 10 seconds.
DTG printing does not limit you by color, although you can only print on cotton t-shirts. Since DTG printing is one of the latest and shiniest technologies on the t-shirt printing playground, it’s pretty expensive. E-commerce platform – If you plan to make money from your custom shirts, you’ll need a way for other people to access them. An e-commerce platform like Shopify does just that, allowing you to advertise your t-shirts and have them find their identity in the apparel market. Blank t-shirts – You’ll need blank t-shirts to apply your designs.
A Heat Press Machine
A high-pressure stream from a showerhead will work well. Focus on the area where the image is and keep spraying until the emulsion in that area has been completely rinsed away. When the timer goes off, remove the glass and image. You should see a faint design right away and the emulsion surrounding the design should be cured hard. It needs to dry in total darkness, so make sure absolutely no light can seep into the area for at least one to three hours.
Look at how to add fonts to your PC, Illustrator, or Photoshop if necessary.If you’re feeling adventurous with design, you can make your own. Make sure any filters you are using on the design are also applied to the font. If you are working with layers on Photoshop, you will need to drag your font layers below the photo effects layers.
What Are The Pros And Cons Of Screen Printing?
The first thing you need when vinyl printing is vinyl. Vinyl typically comes in large and colorful rolled sheets. Once you have the necessary equipment, you’ll find that printing T-shirts at home is very easy and gives you a new sense of flexibility. So read on as we’ll talk about the essential equipment you need to print T-shirts. Low overhead cost on the dye ink and sublimation paper.

You can make your own screen printing set, but it’s best to buy a professional set if you’re on a higher budget since it’ll yield you higher quality prints. A heat press machine is a commercial-grade iron that uses heat to transfer prints. There are different kinds of heat press machines available. There’s the flat surface heat press machine used to print shirts, cotton pillowcases, and many more. Since your prints go directly onto the fabric, you don’t need to over-spend on special transfer paper or transfer a design from paper to garment.
Manufactured by OKI and UniNet, these are office-style full-color printers that have been adapted to use a white toner along with the other colors. The white is what lets you make a transfer that can be applied to dark T-shirts or hardgoods. You ought to clean your screen immediately after you're done printing if you plan to use it again in the future. This is because the screen printing ink tends to dry up pretty fast, and the longer you wait, the harder it becomes to clean it. In case you want to use the screen to print a different image, use an emulsion remover to wipe your screen clean. Finally, it's time to screen print that design onto your t-shirt.

Use a squeegee to help you properly spread the screen. The emulsion ought to cover a slightly larger area than the image you're printing. Repeat the coating for the other side of the screen. You might consider something with one color for your first design. You might also consider using a solid black image so that it excellently blocks out light for the best printing results. Once you have all the above supplies at hand, move on to the next step to learn how to customize your shirts with your preferred design.
Cover the screen with a towel and carry it to your work area. Keep it covered to protect it until you are ready to expose it. Place the screen on the flat black background with the non-recessed part facing upward. Using the HTV method could be useful for you in many ways. You have the option to use glitter and metallic vinyl, and if you plan on using this in small quantities, your production rate will increase.

A design for a sporting team might feature the team colors or the team’s mascot. A design for your band might focus on an image of the band or a graphic that represents the band’s style or sound. Select the type of fabric you want to use based on the weather of your place because in some cases people tend to regret buying good-looking shirts.
This will help your design stick to the t-shirt correctly. The safest option is to use a 100% cotton shirt before experimenting with different fabrics, and a great way to save money is to buy a used t-shirt from a thrift shop. Now transfer the design to your graphics designing software. Quick tip – when you open a file, select the A4 size because it’s suitable.
You’ll need a flat black surface–such as a piece of Bristol board or cardstock–to place your screen on. You’ll also need a light fixture that allows you to direct the light directly down onto the surface. These are general instructions, and there are typically training courses that come with the printers. Clean your screen by spraying it down with cold water from a hose, shower head, or sink; whatever works for you. As you continue cleaning, you'll notice sections where your image lays starting to flake off.
What Do I Need To Print T-Shirts At Home? (2023 Guide)
The printed image needs to completely block all light from going through it. If you hold it up to a light bulb and can see through it, it’s not dark enough. The photo emulsion you purchased has instructions that will tell you exactly how long to expose your image and how far your lightbulb should be from the screen. Read the instructions carefully to ensure you complete the next steps properly.
No comments:
Post a Comment